ETTLINGER recycle le PET
Lors du recyclage, les bouteilles en PET sont broyées et transformées en paillettes, mais la fraction fine qui contient de grandes quantités de polluants est également récupérée et constitue une matière première des plus intéressantes. Les filtres de haute performance ECO de marque Ettlinger permettent d’en extraire du PET débarrassé de ses impuretés, pouvant être transformé pour la fabrication de produits de grande qualité.
Les équipements de recyclage modernes sont capables de concasser les bouteilles en PET (Fig. 1) pour les réutiliser comme matières premières. Une première étape consiste à extraire la fraction légère des matières traitées telle que les films et les étiquettes, puis à les débarrasser des bouchons, des composants en fer blanc et en aluminium. L’étape suivante porte sur la séparation des matières en fonction de leur couleur. Les différentes fractions ainsi constituées sont traitées séparément, broyées, lavées puis récupérées sous forme de paillettes.
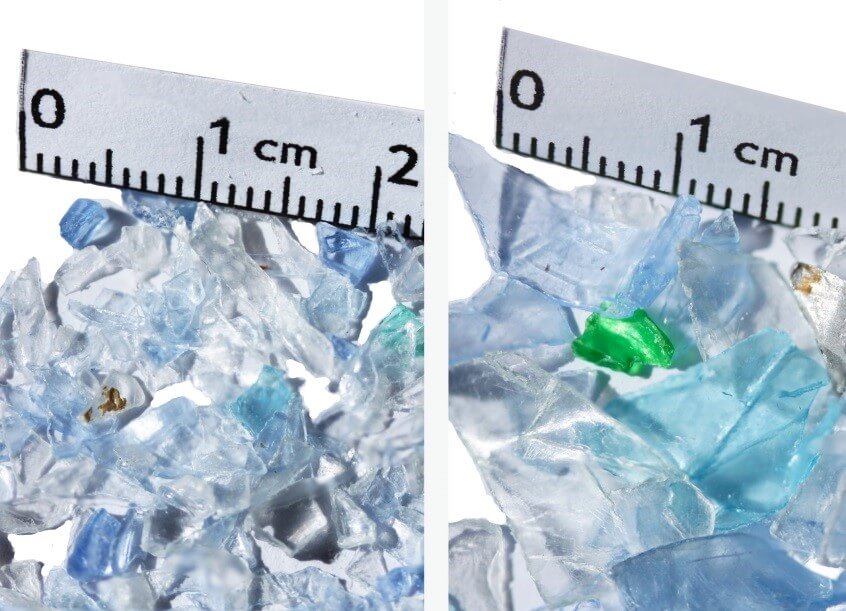
Fig. 1. Bouteilles en PET – une matière première précieuse qui impose des exigences élevées en termes de recyclage. © istockphoto
Lors du broyage des bouteilles, des particules fines de PET mélangées à une grande quantité de polluants tels que des débris de papier, d’aluminium ou de PVC sont séparées des paillettes (Fig. 2).
Alors que les particules fines contiennent par principe des quantités de matières étrangères relativement élevées, les paillettes – malgré les exigences de pureté clairement définies – présentent toujours des écarts entre les valeurs prescrites et la réalité. Pour recycler ces deux fractions de PET, il est nécessaire de filtrer la matière fondue avec une efficacité maximale pendant l’extrusion. Ce n’est qu’à cette condition qu’il sera possible de fabriquer par la suite des produits de haute qualité, utilisables dans les lignes de granulation, de thermoformage et d’emballage.
Les contaminants… un défi pour la filtration
Le degré de pureté des matières broyées varie fortement selon l’installation de recyclage des bouteilles en PET et constitue un défi pour la filtration. Notamment la quantité d’aluminium résiduaire est souvent supérieure à la valeur indiquée dans le tableau (< 10 ppm). La filtration de ces masses en fusion peut engorger rapidement le filtre, causer son usure prématurée et nuire à la rentabilité de l’installation. Ce problème concerne surtout les filtres à rétrolavage issus de la technologie classique. Le nettoyage de ces filtres se fait en inversant le flux de matière fondue. Cette technique s’accompagne d’une perte de matière importante ainsi que de fortes variations de volume et de pression.
Le traitement de cette matière première précieuse que sont les particules fines est autrement plus ambitieux que celui des paillettes. Fortement contaminées, les particules fines nécessitent en amont d’étapes de tamisage et de lavage à chaud pour les débarrasser des particules de papier, d’aluminium ou de PVC. À cela s’ajoute que les particules fines de PET destinées à être réutilisées présentent un teneur très élevée en humidité. De ce fait, et en raison de la présence élevée de PVC, la viscosité intrinsèque IV (comme grandeur de définition du poids moléculaire et comme indicateur du point de fusion, du taux de cristallinité et de la résistance à la traction) diminue fortement, même s’il y a eu un dégazage de bonne qualité pendant la fusion. C’est la raison pour laquelle les particules fines de PET ne sont généralement ajoutées qu’en petites quantités dans certains processus d’extrusion et ce, uniquement si elles sont de très bonne qualité.
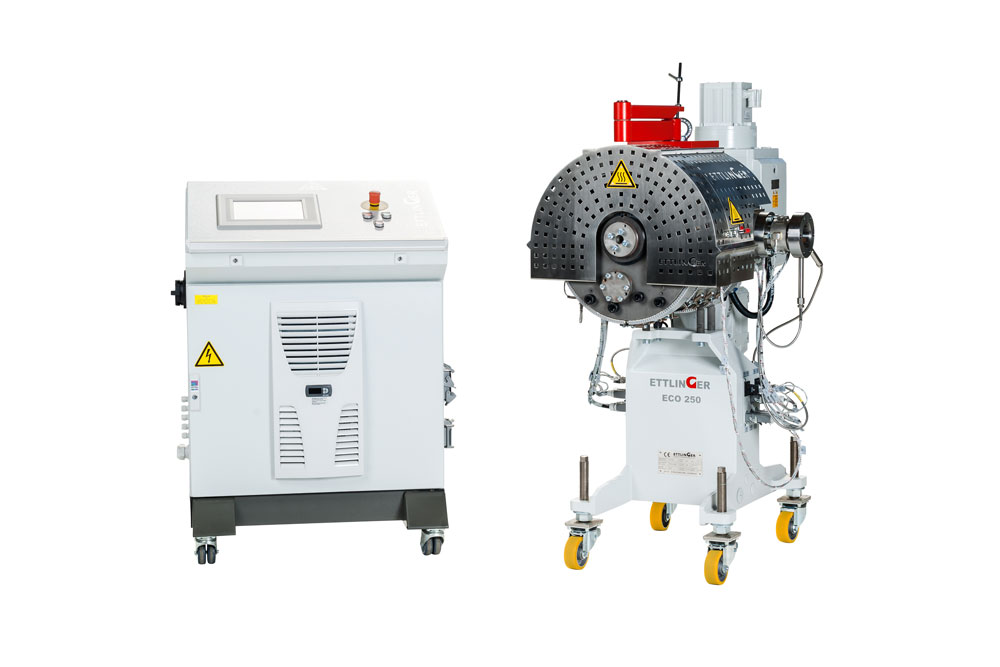
Fig. 3. Ettlinger a optimisé ses filtres ECO pour des débits de 1 500 kg/h (ECO 200) ou de 3 000 kg/h (ECO 250) pour faciliter les processus d’extrusion exigeants tels que la fabrication de films, de plaques et autres produits semi-finis. © Ettlinger
Particules fines de PET exploitables à 100 %
Les fines particules de PET constituent une matière première à haute valeur intrinsèque. Cette matière étant récupérée en grandes quantités lors du recyclage des bouteilles en plastique, son recyclage total se justifie pleinement. La configuration de la vis d’extrusion et du système de dégazage dans l’extrudeuse est d’une importance élémentaire. La mise en œuvre de techniques de filtration capables de fonctionner correctement et de manière rentable en présence de matières de mauvaise qualité avec des teneurs élevées en contaminants est fondamentale.
Les filtres de haute performance de la gamme ECO de l’entreprise Ettlinger répondent parfaitement à ces exigences (Fig. 3). Ils sont conçus spécialement pour fonctionner en continu et séparer les contaminants contenus dans les particules fines de PET pour fournir une masse fondue de grande pureté. Avec leur forme compacte et leurs dimensions peu encombrantes, les systèmes de filtration ECO s’intègrent facilement dans les lignes d’extrusion existantes.
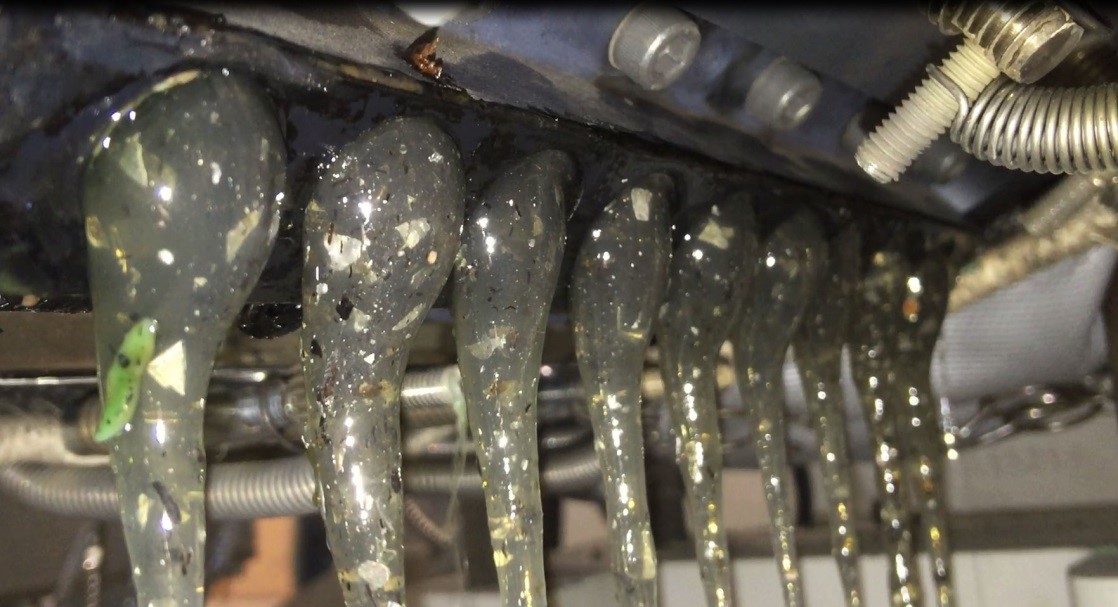
Au cœur de chaque système de filtration, un filtre de forme cylindrique possédant des millions de perforations coniques tourne lentement, entraîné par un servomoteur. La masse en fusion pénètre à l’intérieur du filtre traversant les trous de filtration de différentes tailles. La masse fondue filtrée est évacuée par un système de canaux en direction de la filière. Les contaminants restent agglutinés à l’extérieur du filtre. En dehors des matières solides telles que l’aluminium, les points noirs etc. le filtre retient aussi des substances de masse moléculaire élevée et des matières réticulées résultant des très hautes températures du process.
Une lame de nettoyage racle la surface du tambour en rotation. Les contaminants détachés du tambour sont acheminés vers une vis de déchargement entraînée par un servomoteur puis expulsés hors du système de filtration (Fig. 4). Ce nettoyage continu évite tout risque de colmatage du filtre. Il protège le système contre une pression excédentaire qui pourrait s’exercer à la surface externe du filtre et forcer l’introduction dans le filtre de substances tout d’abord retenues. L’homogénéité de la masse fondue filtrée ne serait plus garantie.
La durée de fonctionnement extrêmement longue, de plusieurs semaines à plusieurs mois, est un élément décisif dans le rapport coût-efficacité. Les pertes minimales de matières contribuent largement à la rentabilité du système et du processus.